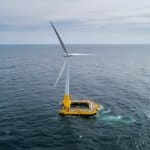
New York approves 2 offshore wind projects totaling 1.7 GW
February 29, 2024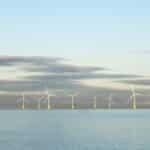
Vaisala, DNV introduce guidelines for Wind Resource Assessment campaigns with dual scanning lidar
March 5, 2024Demonstrator projects show that offshore floating wind is technically proven as a feasible concept. The challenge is how to deliver it for utility-scale projects within the budgets already committed to. Finding a cost-efficient and practical solution that best meets the demands of developers — while also taking into account the perspectives of all stakeholders — is a real conundrum.
The offshore wind players
Finding the answer to this conundrum is not helped by the players waging something akin to a Cold War. An atmosphere of secrecy, suspicion and self-interest overriding a shared objective. Developers, wind turbine OEMs, floating foundation designers and the remaining supply chain all share the common decarbonizing goal but are otherwise competitive and working in isolation from each other.
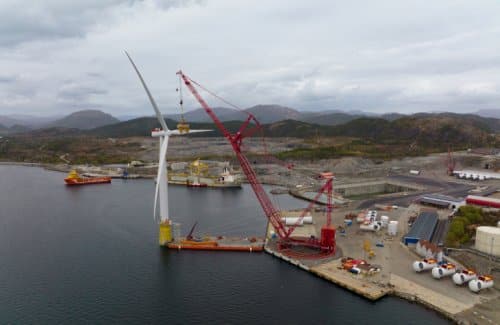
Installation of blades on the second turbine for Hywind Tampen, a floating wind farm under construction in the Norwegian North Sea. Credit: Equinor
Turbine OEMs are in fierce competition and are very guarded of their designs and innovations. Wind turbine generator companies have a revenue stream from fixed wind, but the continuous and unceasing demand for larger generators means the research and development budget to design the next turbine evolution is larger than the profits being generated from current sales.
Most floating foundation designers are designing one possible solution to the floating wind challenge. Their budgets are limited, their investment is at risk and they don’t have all the information they require to design their final commercial offering. The design is therefore generic and not tuned for a specific site and wind turbine generator combination. At the same time, wind turbine components are still increasing in size and weight, and there are unknowns with regards to what a viable mooring solution will be — both factors that will influence the detailed design of any floating foundation. In that respect, it is not possible to say floating foundation designs are optimized to maximize cost efficiency. They are yet to complete the detailed design phase.
The supply chain, including ports, has a golden opportunity with an industry spanning into the next century that is sustainable and will combat global warming. However, this opportunity seems just over the horizon and continuously out of reach. There is no revenue generation available yet for many within that space. Everything is subsidized in a race to be part of a green industry, but people are getting tired of waiting for the industry to get moving. Some are even beginning to question whether the practicalities and costs of offshore floating wind will make it an unviable venture.
Cost efficiency in focus
It is important to remember that cost efficiency is relative. In relation to the design of the floating structure, the scope of requirements will drive the end result. If the critical requirement is to economize and reduce material — and therefore cost — the design will look very different from one where the main focus was to assemble 5,000 tons of steel in a two-day period. And different again to a concrete design to allow for minimal infrastructure and a less-skilled workforce.
It is worth remembering that no single, definitive structure type or floating foundation or mooring configuration will be optimal for every site. There are many variables that will impact the decision, including a technology’s operability, reliability, practicality, readiness, CAPEX, OPEX and potential longevity. A developer must choose a foundation that is most suitable for the wind farm they are developing and, given that many developers’ portfolios are global, that will vary from site to site.
As years of knowledge and learning converge, designs will likely evolve into a shortlist of optimal options for the industry. A balance will be found between conservative design used for early-stage development and disruptive-but-unproven technology.
On top of the theoretical cost efficiency there is a practical side to consider. Access and egress to the floater, connection points for moorings and cables, internal and external inspection of fatigue sensitive connections, and the position of the wind turbine generator onboard are all important considerations that will impact the final design. But perhaps the largest barrier to an acceptable solution is manufacturing — both in terms of the speed at which the structure can be built and where it can be built using local content and skilled labor.
Solving the conundrum
With many variables, the conundrum is hard to solve. The industry needs economy of scale, factory line production and optimized, cost-efficient, fit-for-purpose designs moving toward convergence and standardization. The reality is we are only at the very beginning of this evolution. But what could and should be done to accelerate the commercialization of floating wind?
Developers should be bold and select a floating foundation that best fits their scoring criteria that also has the required technology readiness level. They should also select a wind turbine generator and have designers work together to ensure compatibility. If the development site is known, they can derive everything else from there.
Additional hardware and marine operations may be required than what the project scope allows. For example, the manufacture of the foundations may take longer than expected. In worst case scenarios, if innovation cannot improve efficiency, the costs will have to be absorbed or the project abandoned. Independent, objective strategic and technical consultancy can aid developers in commercializing floating wind — ensuring that costs and risks are minimized, timeframes are realistic, and efficiency is maximized.
Governments could provide the real financial stimulus up front that is needed to break the deadlock, but, unfortunately, they are currently not doing so. They believe it is the developers’ responsibility. Provided the projects do go ahead, then lessons learned over time will determine what works and where further evolution is required.
Being bold and making decisions will kick start the supply chain, ending the chicken-and-egg scenario that is so heavily talked about in the industry. This will provide the confidence to invest and much-needed revenue streams. Floating offshore wind has significant potential as a largely untapped source of renewable energy. However, the industry will need to work together to overcome the cost conundrum it currently faces; it is solvable but demands genuine collaboration between experts.
Filed Under: Featured